
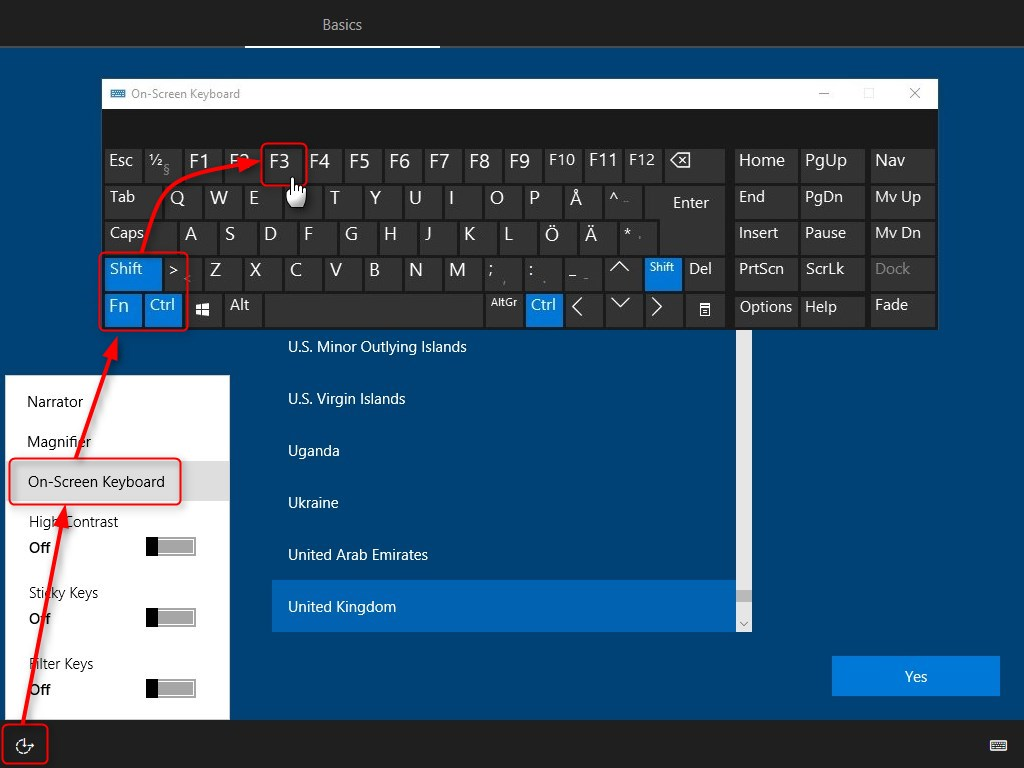

Rectangular cross-section rings are less frequently used. Snap Ring A discontinuous ring that drops into a groove machined into the inside surface of a cell is commonly termed a “snap” ring.1-3 This ring, which acts as a spring, usually has a circular cross section as shown in Figure 6.3. It is difficult to determine exactly when the ring touches the lens surface during assembly so achievement of a particular axial force on the lens is difficult.2 Assembly by this technique is essentially permanent since it is virtually impossible to remove the ring without damaging either it or the lens. The cell and ring materials should have similar thermal expansion coefficients to prevent loosening at extreme temperatures. After installing the lens, the ring can be pressed into place or (preferably) the ring shrunk by cooling and inserted into a cell expanded by heating. The outside diameter (OD) of the ring is made slightly oversize with respect to the inside diameter (ID) of the cell. Interference-Fit Ring A lens can be held against a shoulder or spacer in a cell by an axial force exerted against the lens near its rim by a continuous ring as shown in Figure 6.2. This type of mount also offers some protection against shock and vibration.įIGURE 6.1 Typical configuration of a spring-mounted lens element.
#FLYCUT EQUIVALENT FOR WINDOWS FREE#
Free circulation of air around the lens is allowed. Symmetry of the cantilevered springs tends to keep the lens centered. Three flat springs spaced at 120° intervals around the lens rim are shaped to interface with that rim. Spring Suspension In applications involving large temperature changes with loose centration, tilt, and/or axial positioning tolerances, lenses might be supported by springs.1,2 One such mounting, typically used to support condenser lenses or filters made of heat-absorbing glass in projector illuminators, is illustrated in Figure 6.1. For simplicity, it is assumed in most cases that the lenses are glass and the mount is a simple, cylindrical metal cell. Although the examples show single lens elements, some of these concepts are applicable to multiple element designs. In each case, the parts are premachined to specified dimensions and assembled without adjustment. Principles of optomechanical design and material selection intended to minimize the adverse effects of these imposed forces while retaining component function, location, and alignment are explained.Ħ.2 Mounting Lenses Low Precision Mounts In this section, configurations for relatively low cost, low precision mounts for lenses are considered. Analytical relationships are given for estimating selected important attributes of the designs such as contact stress due to forces imposed during assembly or due to temperature changes or acceleration. Numerous examples from the literature illustrate these techniques.
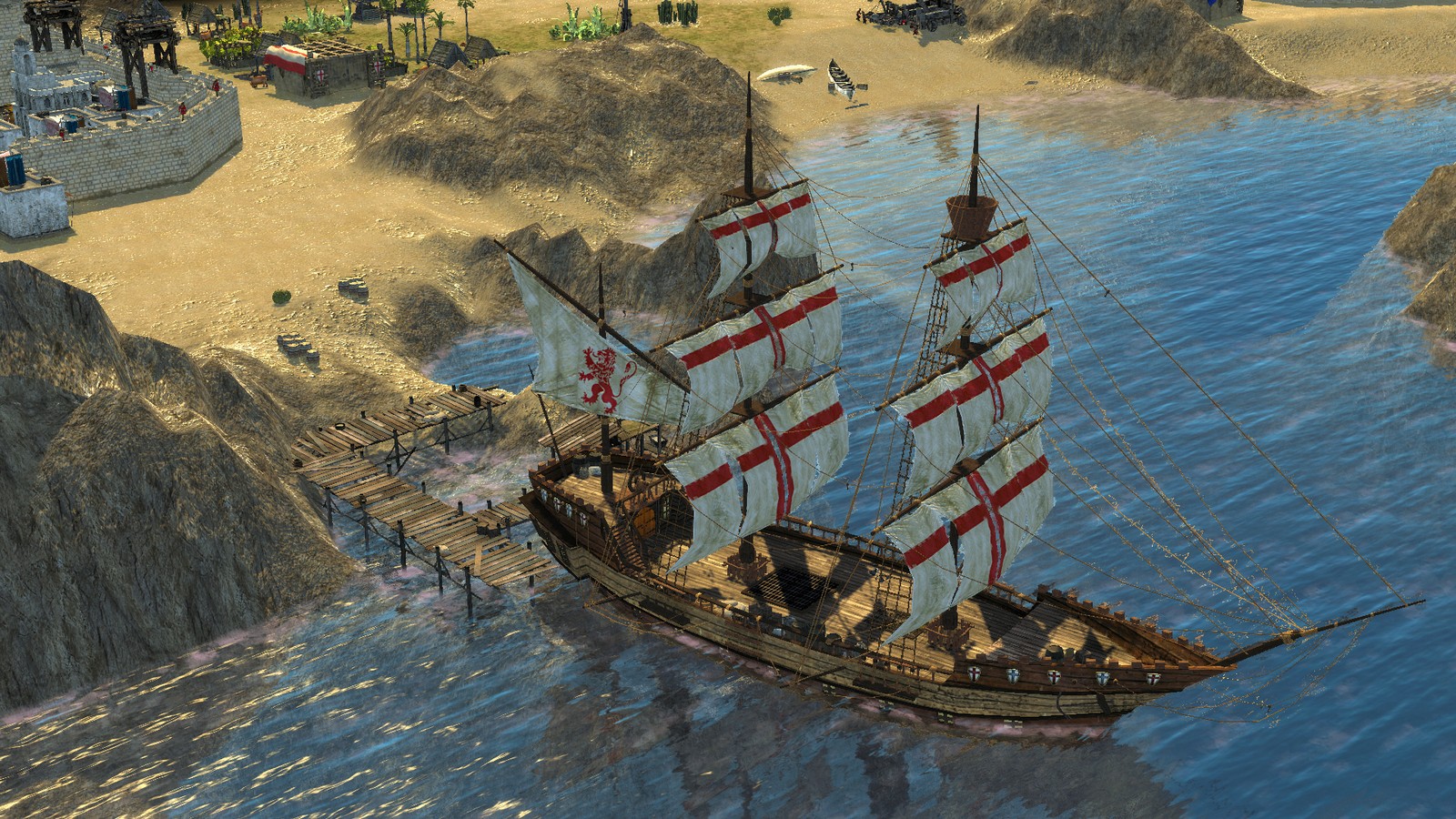
